Answer: It may be that the fit between the inner hole of the bearing and the shaft is loose, resulting in slippage between the inner ring and the shaft, causing the inner ring and the shaft to sinter together due to high temperature. Reference solution: Depending on the bearing type, the standard bearing is made of hardened and induction hardened heat-treated steel, and the recommended maximum operating temperature is between 120 and 200 degrees. If the bearing is required to continuously operate at high temperature, the dynamic load capacity of the bearing may need to be adjusted. Also pay attention to the role of lubricants. Bearing material, working environment, lubricant, etc. should be paid attention to.
2. Generally, everyone says to choose C3 clearance. What data is it? Can you be specific? How to determine, how to detect? Answer: Bearing clearance refers to the amount of movement when one side of the inner ring or outer ring is fixed when the bearing is not installed, and then the unfixed side moves radially or axially. According to the moving direction, it can be divided into radial clearance and axial clearance. The size of the clearance during operation (called working clearance) has an impact on the rolling fatigue life, temperature rise, noise, vibration and other properties of the bearing. The radial clearance of rolling bearings is generally divided into /C1, /C2, /C0, /C3, /C4, /C5 groups.
Groups 1 and 2 belong to the small clearance; Group 0 is the standard clearance; Groups 3, 4, and 5 are the larger clearance. The choice of the rolling bearing clearance group should be selected according to the corresponding standards according to the product type, size, temperature of use, and the tightness of the fit with the shaft and the hole. Of course, this is a problem that should be determined when the equipment is selected. The inspection of clearance should also be professionally inspected according to relevant industry standards.
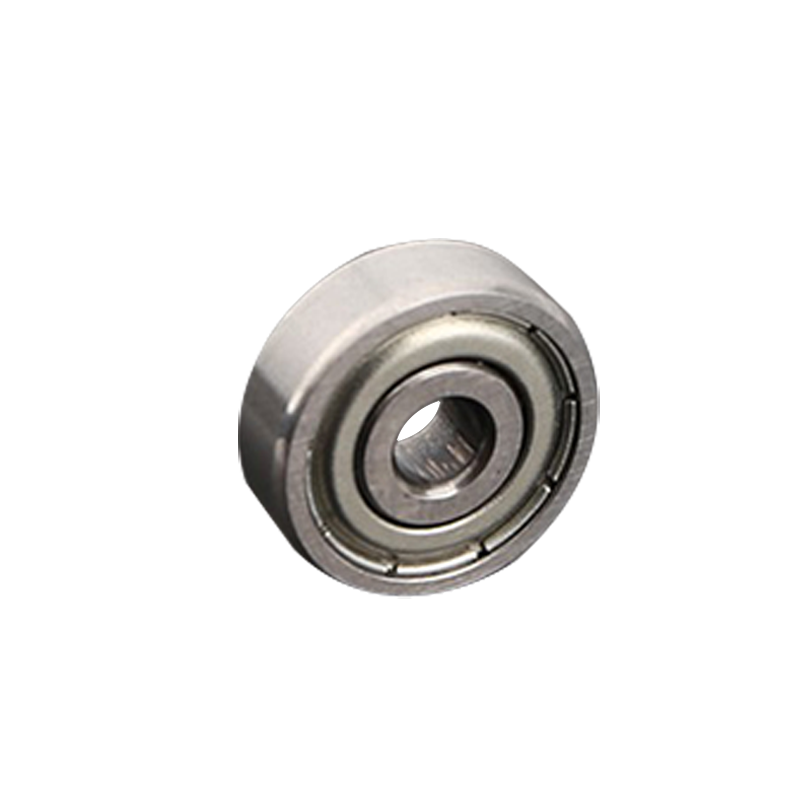